Why Are Screening Buckets Used for Backfilling?
- Gyru-Star Team
- Mar 26
- 4 min read

Backfilling and padding are essential steps in utility installation, protecting underground cables and pipes from sharp debris and ensuring long-term durability. Traditionally, contractors have relied on screened soil or sand for this purpose, but rising material and transport costs have made onsite recycling a more attractive alternative. Screening buckets offer a cost-effective and highly mobile solution, allowing contractors to screen excavated material directly at the jobsite.
What is Cable and Pipe Padding?
Padding material is used to protect underground utilities from potential damage caused by stones or debris. While requirements vary depending on location, sand and screened soil are the most commonly used materials. Many contractors opt to reuse excavated trench material (trench arisings) as padding, but it must first be screened to ensure a consistent, high-quality product. This is where screening buckets come into play, transforming waste material into a usable resource while reducing costs and environmental impact.
Why Use a Screening Bucket?
Here’s three reasons why you may want to considering using a screening bucket for padding and backfilling.
Access Any Jobsite
One of the biggest challenges for utility contractors is jobsite accessibility. Mobile pipeline padders and traditional screening plants are often too large for remote or confined locations, making material handling and transport a logistical challenge. Screening buckets eliminate this issue by allowing material to be processed exactly where it’s needed, right at the trench. If the carrier can access the jobsite, so can the screening bucket.
Urban Jobsites
Working in built-up areas comes with unique challenges, such as limited space, strict emissions regulations, and noise restrictions. Screening buckets, such as the Gyru-Star E Series, can turn excavators as small as 1 ton into powerful mobile backfilling machines. This is ideal for jobsites with restricted access or when working in close proximity to traffic or pedestrians.
Gyru-Star buckets also help contractors comply with strict environmental regulations by eliminating the need for diesel-powered screening plant or padding machines. All models are fully compatible with electric and hydrogen-powered carriers. Additionally, thanks to their carbon belt drive system, Gyru-Star screening buckets operate far more quietly than traditional chain-driven models, making them the perfect solution for noise-sensitive urban projects and night work.
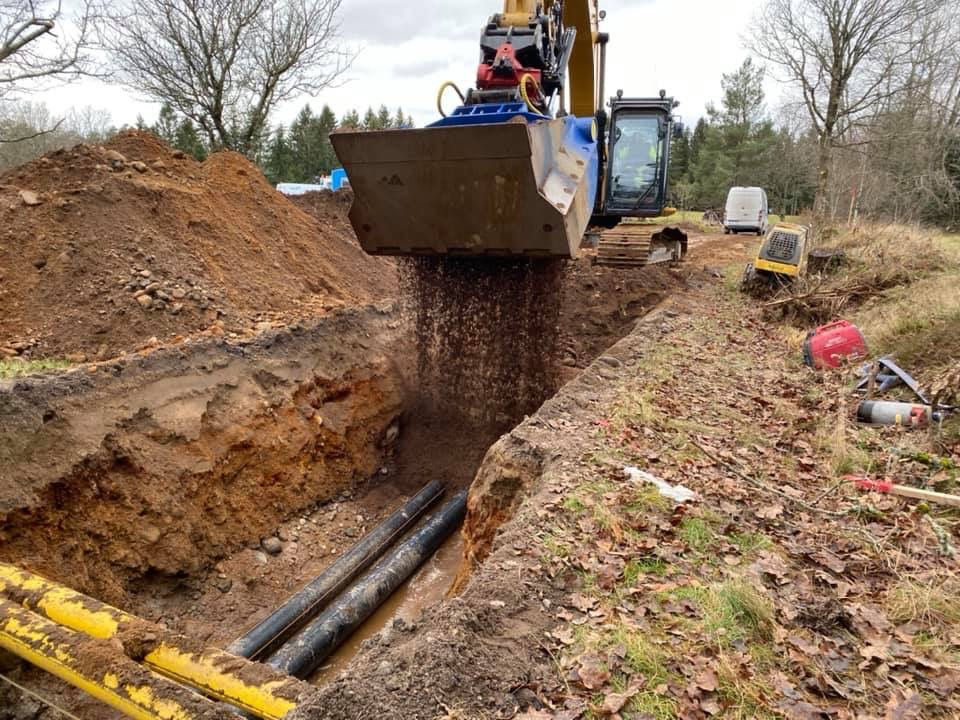
Remote Jobsites
Many of the same benefits for urban projects also apply to those in remote areas. The ability of screening buckets to go anywhere the carrier can allows contractors to work miles from the nearest road, whilst making transport to these areas faster, easier and cheaper.
Screening buckets also combine the screening and backfilling process into a single operation, allowing one excavator, loader or skid steer to do the work of two machines.
Streamline Your Operations
Keeping projects on schedule and within budget is always a challenge. Screening buckets simplify backfilling operations by reducing equipment costs, minimising material handling, and combining multiple processes into one. Instead of investing in specialist, single-application machinery, contractors can use screening buckets with the machines they already have onsite.
Screening material at the trench eliminates the need for transporting materials across or offsite, reducing fuel consumption and project delays. It also cuts down the number of machines and operators required, which significantly lowers operational costs.
Gyru-Star screening buckets are also known for their ultra-low maintenance requirements, thanks to their self-tensioning carbon belt drives.
Reduce Your Environmental Impact
With many projects now required to meet strict environmental targets, using a screening bucket for backfilling can significantly reduce a contractor’s carbon footprint. By processing material onsite, contractors minimise vehicle movements, reducing fuel consumption and emissions. Fewer machines operating onsite also mean less ground disturbance, preventing soil compaction and protecting the surrounding environment.
Why Choose Gyru-Star?
True Screening®
Gyru-Star screening buckets are True Screening® solutions, meaning they screen material without crushing or shredding. This ensures that oversize material, debris and stones are completely removed rather than broken down and mixed into the product.
Compatibility
With 31 models across six series, Gyru-Star offers the largest range of polyurethane star screening buckets on the market. Whether you're working with a 1-ton or 30-ton excavator, there's a Gyru-Star model purpose built for your machine. Each bucket is optimised for a specific carrier weight range, ensuring maximum efficiency with any machine.
Strength and Durability
Durability is key, especially in remote locations where equipment failures can cause significant delays. Gyru-Star screening buckets feature a multi-layer monocoque shell reinforced with HB400 wear-resistant steel, providing exceptional strength without unnecessary weight. The self-tensioning carbon belt drives require no adjustments or lubrication, ensuring long-term reliability.
No Risk of Contamination
Unlike traditional screening equipment that relies on oil baths or exposed drivelines, Gyru-Star buckets use fully sealed bearings and lubrication-free carbon belt drives. This eliminates the risk of oil or grease contaminating the screened material, making them perfect for projects with strict environmental controls.
All-Weather Performance
Gyru-Star screening buckets come equipped with a stainless steel non-stick floor, preventing blockages and ensuring a continuous flow of material into the rotors. Combined with our True Screening® technology, this allows contractors to screen and backfill in all weather conditions, keeping projects on track year-round.
Turn Your Liabilities into Assets
For contractors working on underground utilities, Gyru-Star screening buckets offer an efficient, cost-effective, and environmentally friendly backfilling solution. Whether operating in urban environments, remote locations, or anywhere in between, their ability to screen material onsite reduces waste, cuts costs, and minimises your environmental impact.
Want to learn more about our innovative screening solutions? Get in touch with our team today or contact your local Gyru-Star dealer.
Comments